نگهداری و تعمیرات مبتنی بر قابلیت اطمینان (RCM) چیست؟
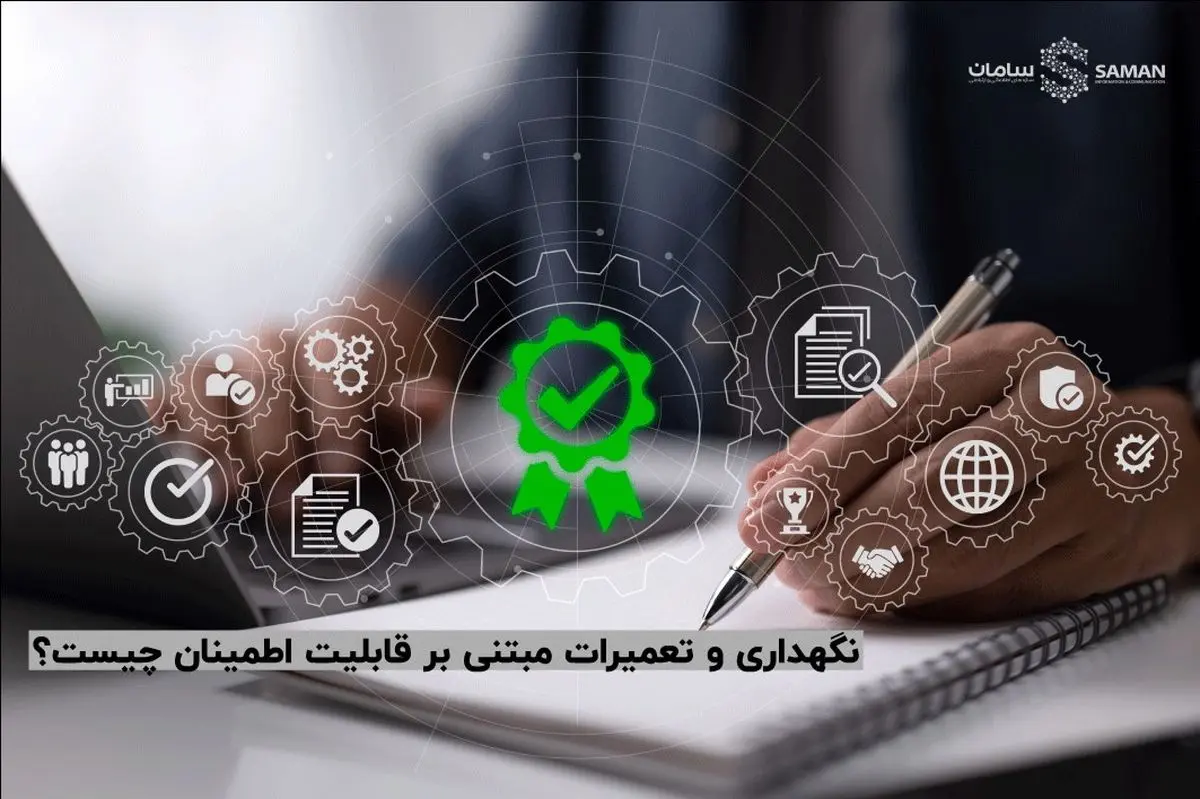
نگهداری و تعمیرات مبتنی بر قابلیت اطمینان (RCM) یک استراتژی تعمیر و نگهداری در سطح شرکت است که برای بهینهسازی برنامه تعمیر و نگهداری آن شرکت یا تأسیسات اجرا میشود. نتیجه نهایی برنامه RCM اجرای یک استراتژی نگهداری خاص در هر یک از داراییهای تاسیسات است. استراتژیهای تعمیر و نگهداری برای حفظ بهرهوری کارخانه با استفاده از تکنیکهای نگهداری مقرون به صرفه بهینه شدهاند.
تعمیر و نگهداری مبتنی بر قابلیت اطمینان کجا استفاده میشود؟
تعمیر و نگهداری مبتنی بر قابلیت اطمینان در صنعت هوانوردی آغاز شد، که هنوز روشی مهم در این صنعت باقی مانده است. این عمل در صنایع دیگری از جمله موارد زیر محبوبیت پیدا کرده است.:
• ساخت تجهیزات نظامی
• انرژی هستهای
• تولید فولاد
• حمل و نقل هوایی
• بهداشت توزیع مواد غذایی
• تولید دارو
RCM یا نگهداری و تعمیرات مبتنی بر قابلیت اطمینان همیشه در مواردی با احتمال عواقب شدید استفاده میشود. مثلا نقص در تولید یک دارو میتواند هزاران مصرف کننده را تحت تاثیر قرار داده و باعث آسیب، بیماری، یا حتی مرگ شود. به همین دلیل است که تولیدکنندگان دارو استراتژی RCM را اجرا میکنند.
چهار اصل مهم در برنامه تعمیر و نگهداری مبتنی بر قابلیت اطمینان عبارتند از:
1. هدف اصلی حفظ عملکرد سیستم است
2. شناسایی حالتهای خرابی که میتواند بر عملکرد سیستم تأثیر بگذارد
3. اولویت بندی حالتهای خرابی
4. انتخاب وظایف قابل اجرا و موثر برای کنترل حالتهای خرابی
مزایا
پیادهسازی نگهداری و تعمیرات مبتنی بر قابلیت اطمینان RCM در دسترس بودن تجهیزات را افزایش داده و هزینههای نگهداری و منابع را کاهش میدهد. نرم افزار CMMS نمونهای از ابزارهای است که هزینههای تعمیر و نگهداری را تا 40 درصد کاهش میدهند. هزینه تعمیر و نگهداری، خطر آسیب و خرابی احتمالی جزو عوامل موثر در اجرای RCM برای تاسیسات میباشد.
معایب
RCM هزینه کل مالکیت و نگهداری یک دارایی را در نظر نمیگیرد. هزینههای اضافی مالکیت، مانند هزینههای نگهداری مبتنی بر شواهد، در نظر گرفته نشده و بنابراین در ملاحظات نگهداری لحاظ نمیشوند.
چگونه استراتژی تعمیر و نگهداری کاملا متعادلی را ایجاد میکنید؟
فرآیند RCM: هفت مرحله برای اجرای تعمیر و نگهداری مبتنی بر قابلیت اطمینان
چندین روش مختلف برای اجرای تعمیر و نگهداری مبتنی بر قابلیت اطمینان وجود دارد که در هفت مرحله زیر خلاصه شده است.
مرحله 1: انتخاب تجهیزات برای بررسی RCM
اولین قدم، انتخاب یک قطعه از تجهیزات برای بررسی تعمیر و نگهداری مبتنی بر قابلیت اطمینان است. تجهیزات انتخاب شده باید از نظر تأثیر بر عملیات، هزینه تعمیرات اولیه، و هزینههای اولیه تعمیر و نگهداری پیشگیرانه حیاتی باشد.
مرحله 2: تعریف مرزها و عملکرد سیستمهای مشمول تجهیزات انتخاب شده
این تجهیزات متعلق به سیستمی هستند که عملکرد مهمی را انجام میدهد. سیستم میتواند بزرگ یا کوچک باشد، اما عملکرد و ورودیها و خروجیهای آن باید مشخص باشند. مثلا وظیفه سیستم تسمه نقاله، حمل و نقل کالا است. ورودی کالا و انرژی مکانیکی تسمه را تغذیه میکنند، در حالی که خروجی، کالاهایی است که در انتهای دیگر قرار دارند. در این حالت موتور الکتریکی تامین کننده انرژی مکانیکی به عنوان بخشی از سیستم متفاوت در نظر گرفته میشود.
مرحله 3: حالتهای خرابی (تعریف راه هایی را که در آن سیستم ممکن است از کار بیفتد)
در مرحله 3، هدف فهرست کردن تمام راههای نقص در عملکرد سیستم است. مثلا تسمه نقاله ممکن است به دلیل ناتوانی در حمل کالا از یک سر به سر دیگر از کار بیفتد یا کالا را با سرعت کافی جابجا نکند.
مرحله 4: شناسایی علل اصلی حالتهای خرابی
با کمک اپراتورها، تکنسینهای مجرب، کارشناسان RCM و کارشناسان تجهیزات، میتوان علل اصلی هر حالت خرابی را شناسایی کرد. دلایل اصلی خرابی تسمه نقاله میتواند شامل عدم روانکاری روی غلتکها، خرابی بلبرینگ یا شل شدن تسمه باشد.
از این الگو استفاده کنید و ساعتها را برای بررسی علت اصلی تلف نکنید.
مرحله 5: ارزیابی اثرات نقص در عملکرد
در این مرحله اثرات هر حالت نقص در نظر گرفته میشود. خرابی تجهیزات میتواند بر ایمنی، عملیات و سایر تجهیزات تأثیر بگذارد. بحرانی بودن هر یک از این حالتهای خرابی را نیز میتوان در نظر گرفت.
تکنیکهای پیشنهادی مختلف مورداستفاده برای ارائه یک رویکرد سیستماتیک برای این مرحله عبارتند از:
1. بررسی حالت شکست و تجزیه و تحلیل اثرات (FMEA)
2. بررسی شکست، حالت، اثر و تحلیل بحرانی
3. مطالعات خطر و قابلیت بهره برداری (HAZOPS)
4. تجزیه و تحلیل درخت خطا (FTA)
5. بازرسی مبتنی بر ریسک (RBI)
مهمترین حالتهای شکست در پایان این تحلیل سیستماتیک مشخص خواهد شد. سوالات زیر را از خود بپرسید: «آیا این حالت خرابی پیامدهای ایمنی دارد؟» و «آیا این حالت خرابی منجر به قطع کامل یا جزئی عملیات میشود؟». پاسخ شما مهمترین حالتهای شکست برای اولویتبندی برای بررسی بیشتر است. نکته مهم، حالتهای خرابی که حفظ میشوند، فقط شامل مواردی میشوند که احتمالاً در شرایط عملیاتی واقعی رخ میدهند.
مرحله 6: انتخاب تاکتیک تعمیر و نگهداری برای هر حالت خرابی
در این مرحله مناسبترین تاکتیک نگهداری برای هر حالت خرابی مشخص میشود. تاکتیک نگهداری انتخابی باید از نظر فنی و اقتصادی امکان پذیر باشد.
تعمیر و نگهداری مبتنی بر شرایط زمانی انتخاب میشود که تشخیص شروع یک حالت خرابی از نظر فنی و اقتصادی امکانپذیر باشد.
تعمیر و نگهداری پیشگیرانه مبتنی بر زمان یا مبتنی بر استفاده، زمانی انتخاب میشود که از نظر فنی و اقتصادی امکان کاهش خطر خرابی با استفاده از آن روش وجود داشته باشد.
برای حالتهای خرابی که گزینههای نگهداری و تعمیر پیشگیرانه مبتنی بر شرایط رضایت بخشی ندارند، طراحی مجدد سیستم برای حذف یا اصلاح حالت خرابی باید در نظر گرفته شود.
حالتهای خرابی که در مرحله 6 به عنوان بحرانی شناسایی نشدهاند، میتوانند در این مرحله به عنوان کاندیدهای مناسب برای برنامه تعمیر و نگهداری از اجرا تا خرابی شناسایی شوند.
مرحله 7: اجرای تاکتیک تعمیر و نگهداری انتخاب شده و سپس بررسی منظم آن
نکته مهم این است که روش RCM تنها در صورتی مفید خواهد بود که توصیههای تعمیر و نگهداری آن عملی شود. پس از انجام این کار، مهم است که توصیهها به طور مستمر بررسی و با کسب اطلاعات بیشتر به روز شوند.
تأثیر تعمیر و نگهداری مبتنی بر قابلیت اطمینان
محصول نهایی بررسی RCM به خوبی اجرا شده، انتخاب یک استراتژی تعمیر و نگهداری مناسب برای هر قطعه از تجهیزات است، لذا اثر آن بهبود قابلیت اطمینان کلی است. هدف RCM کاهش هزینهها، بهبود ایمنی و حذف وظایف تعمیر و نگهداری بیهوده قطعات ماشین آلات است. پیادهسازی فرآیندهای RCM مانع از تکرار ذهنیت یکسان و نهایتاً هدررفت زمان و منابع ارزشمند میگردد.
نتیجه نهایی
مستلزم اجرای استراتژی RCM وجود سیستم نگهداری و تعمیرات است، این نرم افزار بایستی قابلیت پیاده سازی انواع استراتژی تعمیر و نگهداری را داشته باشد. همانطور که اشاره شد، تعمیر و نگهداری مبتنی بر قابلیت اطمینان با ترکیب انواع استراتژی تعمیر و نگهداری بهترین استراتژی را در تجهیز یا قطعه بکار میگیرید. نرم افزار تعمیر و نگهداری آلکا با تجربه 15 ساله (از سال1386) استراتژی های پرکاربرد و کارآمد را مختص کسب و کارهای کشور ایران را ارائه کرده است. این نرم افزار هم اکنون در شرکت بزرک تولیدی، عمرانی، معدنی، کشاورزی، لجستیک و ... مورد بهرهبرداری قرار گرفته است. برای کسب اطلاعات بیشتر و بررسی کلی امکانات نرم افزار می توانید در خواست دمو نرم افزار نگهداری و تعمیرات را در سایت pmem.ir ثبت نمایید .