سرپرست معاونت بهره برداری شرکت فولاد هرمزگان مطرح کرد:
دستیابی فولاد هرمزگان به بالاترین بهرهوری در واحدهای تولیدی/ برنامه بلندمدت برای بهره وری منابع انرژی در دستور کار فولاد هرمزگان است
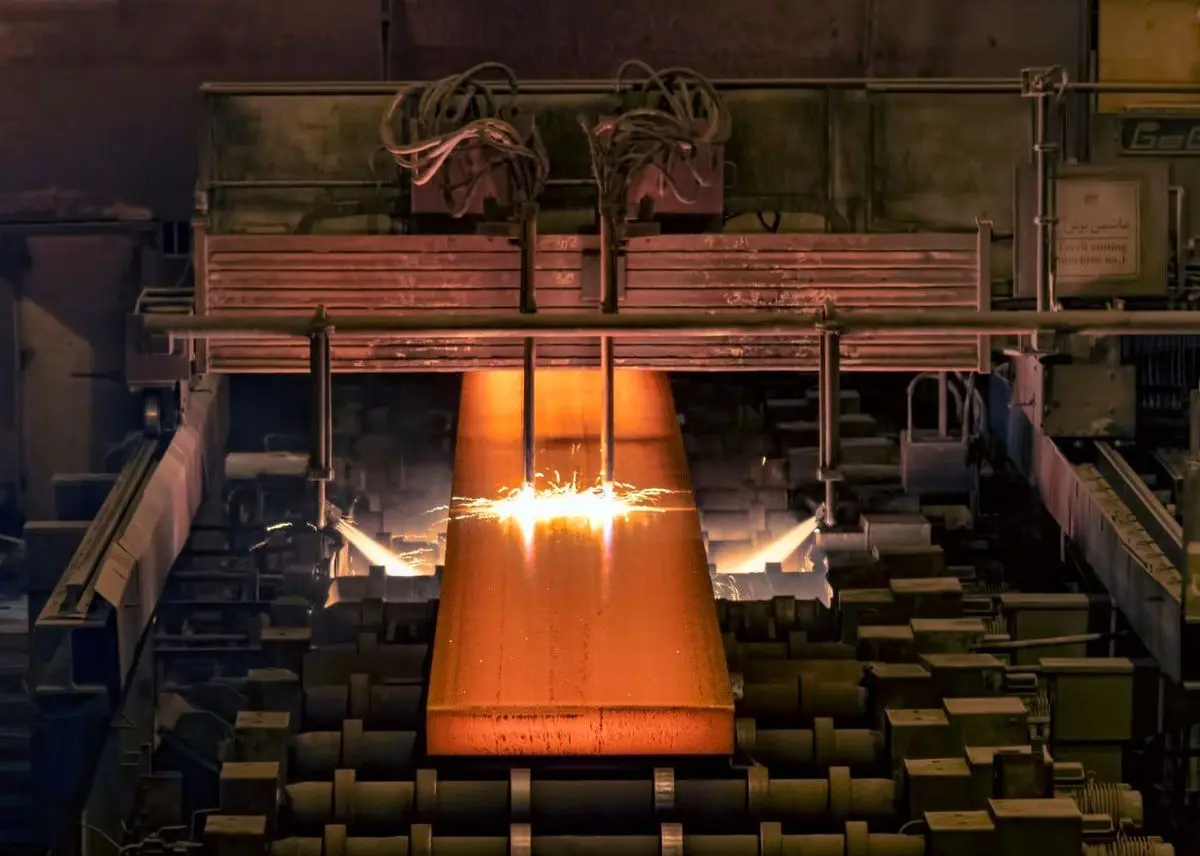
شرکت فولاد هرمزگان توانسته با اقدامات گستردهای که در خصوص استفاده بهینه از منابع، زیرساختها و انرژی انجام دهد، به بالاترین بهرهوری تولید هم در واحد فولادسازی و هم در واحد احیا مستقیم دست پیدا کند.
به گزارش ایلنا به نقل از روابط عمومی شرکت فولاد هرمزگان، مجید ابوعطیوی سرپرست معاونت بهرهبرداری شرکت فولاد هرمزگان با بیان این مطلب و درباره اقدامات صورت گرفته در حوزه بهینهسازی مصرف انرژی و کاهش هزینهها در فرآیند تولید گفت: با توجه به ناترازی انرژی که شرکتهای فولادی این روزها با آن دست و پنجه نرم میکنند، برنامهریزی و اقدامات گستردهای در دستور کار فولاد هرمزگان قرار گرفته تا به سمت بهرهوری هرچه بیشتر منابع و انرژی پیش رود که میتوان به مواردی همچون تعیین ناحیه بهرهبرداری به عنوان دامنه استقرار سیستم مدیریت انرژی ISO50001-2018، تعیین حد مصرف انرژی تجهیزات تولیدی، پایش و کنترل مصارف در واحدهای تولیدی و تعیین تجهیزات بارز انرژی در واحدهای تولیدی اشاره کرد.
ابوعطیوی با اشاره به ثبت رکوردهای تولید در مواقع بدون محدودیت انرژی، عنوان کرد: با انجام پروژههای بهبود متعدد در سالهای گذشته و استفاده از دانش و تجربیات کارکنان رکوردهایی را در فولادسازی به میزان 165 هزار تن تختال و احیا مستقیم به میزان 173 هزار تن به ثبت برسانیم که به ترتیب 32 و 26 درصد بیش از ظرفیت اسمی این واحدها بوده و به جرات میتوان گفت که این رکوردها در صنعت فولاد کشور بیش از ظرفیت اسمی بینظیر هستند.
وی افزود: پایش و کنترل موکد بر مصارف حاملهای انرژی در تجهیزات از طریق کنترل عملیات، کنترل و پایش تامین اقلام موثر بر انرژی از طریق روش اجرایی مربوطه، پایش کالیبراسیون تجهیزات ابزار دقیق تجهیزات، تعریف خطوط مبنا جهت پیشبینی مصارف و تعیین اهداف خرد و کلان انرژی و تعریف پروژههای بهبود در راستای بهبود مستمر عملکرد از جمله اقداماتی است که در راستای کاهش هزینهها و بهینهسازی مصرف در دستور کار قرار دارند.
به گفته وی، روشهای خاصی برای اندازهگیری و مدیریت مصرف در خط تولید وجود دارد که میتوان به تعیین انرژیهای بارز واحدهای تولیدی از طریق روش پارتو، تعیین تجهیزات، تعریف خطوط مبنای انرژی جهت پیشبینی مصارف و تعیین اهداف خرد و کلان انرژی و پایش مصارف واحدهای تولیدی از طریق مقایسه با خط مبنای انرژی و صدور اقدام اصلاحی در صورت نیاز اشاره کرد.
شناسایی نقاط قابل بهبود
سرپرست معاونت بهرهبرداری فولاد هرمزگان گفت: ما در فولاد هرمزگان برای شناسایی نقاط بهبود در مصرف روشهای مختلفی داریم که از جمله مهمترین آنها اندازهگیری مصارف کلیه حاملهای انرژی در واحدهای تولیدی، یکپارچهسازی و تبدیل به واحد ژول جهت تعیین سهم مصرف هر کدام از حاملهای انرژی، تعیین میزان انرژیهای بارز واحدهای تولیدی از طریق روش پارتو، تعیین تجهیزات و پایش و کنترل موکد مصارف حاملهای انرژی در تجهیزات از طریق کنترل عملیات است.
وی افزود: همچنین شناسایی پارامترهای موثر برعملکرد انرژی تجهیزات، شناسایی فرصتهای بهبود و اولویتبندی فرصت بهبود و تعریف پروژههای بهبود نیز برای این موضوع تعریف شده اند.
مدیریت مصرف انرژی در فولاد هرمزگان
ابوعطیوی به آموزش کارکنان در زمینه مدیریت مصرف انرژی و بهینهسازی فرآیندها اشاره کرد و افزود: تعیین تجهیزات بارز، تعیین مشاغل مرتبط با تجهیزات، ارسال لیست مشاغل موثر بر انرژی به واحد سازماندهی و طبقهبندی مشاغل جهت ایجاد شایستگیهای مرتبط با مدیریت انرژی در شرح شغل این مشاغل و برگزاری آموزشهای لازم جهت احراز شایستگی مدیریت انرژی برای مشاغل موثر برای این موضوع در نظر گرفته شده است.
وی تصریح کرد: با توجه به اینکه تعرفههای برق و گاز در مقایسه با سال 1402 افزایش چشمگیری داشته که باعث افزایش هزینههای انرژی میشود، همچنین اعمال محدودیتهای شدیدتر در سال 1403 باعث کاهش میزان تولید و افزایش مصارف انرژی به ازای تن محصول تولیدی شد، اما شرکت فولاد هرمزگان با اجرای اقدامات و پروژههای بهبود، تلاش کرده تا اثرات منفی موارد فوق را به حداقل برساند که برخی از آنها در ادامه آمده است:
• اجرای اثربخش نظام مدیریت انرژی براساس استاندارد ISO 50001:2018
• برنامهریزی تعمیرات در زمان اعمال محدودیتهای انرژی
• آموزش کارکنان و فرهنگسازی مصرف بهینه انرژی
• کاهش مصرف برق کورههای قوس الکتریکی از طریق کاهش مصرف سرباره سازها، بهبود کیفیت سرباره، کاهش توقفات بین ذوبها، کاهش زمان مستقیم کاری کورهها و افزایش سرعت شارژ مواد به کورههای قوس الکتریکی
• کاهش مصرف ویژه انرژی در واحد آهنسازی با کاهش توقفات اضطراری ناشی از اجرای مؤثر رویکرد مدیریت تجهیزات تولیدی و اجرای تعمیرات اساسی
• کاهش مصرف برق واحد آب شیرین کن با اجرای پروژه اصلاح سیستم پیش تصفیه
• کاهش هزینه برق با متناسبسازی میزان خرید برق با مصرف واقعی پایان ماه در قرار داد دو جانبه
• کاهش هزینه گاز طبیعی با تفکیک هزینههای گاز واحدهای فولادسازی و احیا مستقیم
استفاده از منابع انرژی تجدیدپذیر و فناوریهای نوین
به گفته ابوعطیوی، استفاده از منابع انرژی تجدید پذیر در دستور کار قرار دارد و شرکت فولاد هرمزگان در حال نصب نیروگاه خورشیدی 600 مگاواتی از طریق هلدینگ فولاد مبارکه است که 30 درصد از سهام این نیروگاه متعلق به فولاد هرمزگان بوده و 120 مگاوات از این نیروگاه به بهرهبرداری رسیده و به شبکه برق تزریق شده است.
وی در پاسخ به این سوال که آیا از فناوریهای نوین برای افزایش بهرهوری در خط تولید استفاده میشود نیز اظهار کرد: بله ما از مدل شبکه عصبی و دادهکاوی برای تشخیص عیوب تختال در مرحله کنترل کیفی استفاده میکنیم. با این ماژول بازرس کنترل کیفیت، عیوب تشخیص داده شده توسط مدل شبکه عصبی باید بررسی و پاسخ دهد. همچنین از Data Analytics برای تعیین پارامترهای تولید آهن اسفنجی استفاده میشود. از سوی دیگر به منظور حفظ ایمنی کارکنان در خط تولید از فناوری پردازش تصویر برای تشخیص مغایرتهای ایمنی استفاده میکنیم.
سرپرست معاونت بهرهبرداری شرکت فولاد هرمزگان افزود: همچنین دستیار هوش مصنوعی براساس مدلهای تجاری ChatGPT، DeepSeekو Gemini در دسترس کلیه کاربران سازمان بدون نیاز به اینترنت و محدودیتهای شارژ به صورت نامحدود قرار دارد و کاربران میتوانند در تحلیلی مسائل خود از این فناوریها استفاده کنند و نتیجه استفاده از آن در کاهش زمان رسیدن به تصمیمات اثربخش بوده است و بدون استفاده از آنها کارکنان باید بر مبنای خبرگی خود تصمیماتی را اتخاذ میکردند.
وی تصریح کرد: اما در این میان استفاده از فناوری اینترنت اشیا به دلیل محدودیتهای زیرساختی، استفاده از این فناوری هنوز به بهرهبرداری نرسیده است؛ اما پروژههای مختلفی برای ایجاد امکان استفاده از این تکنولوژی در دست اقدام است. از جمله این پروژهها میتوان به طراحی و استقرار زیرساخت کارخانه متصل، طراحی مدل عملیاتی دیجیتال، ساخت پلتفرم کارخانه دیجیتال و… اشاره کرد.
به گفته وی، با استفاده از فناوریهای نوین، ریشهیابی علل مشکلات تسهیل شده است و میتوان به حل مسئله تولید با رویکرد تحلیل کسب و کار اشاره کرد که با کمک مشاورین خبره و مسلط به مفاهیم تحلیل داده، انجام شده و از نمونههای موفق در این زمینه استفاده از فناوری بینایی ماشین در تشخیص مغایرتهای ایمنی، استفاده از هوش مصنوعی در تشخیص عیوب را نام برد که قابلیت اشتراکگذاری را دارند.
مدیریت ضایعات مواد اولیه در کارخانه
به گفته ابوعطیوی، شرکت فولاد هرمزگان در راستای تحلیل و مدیریت ضایعات مواد اولیه سیستمهای پایش و کنترل کیفیت به منظور شناسایی و کاهش ضایعات را پیادهسازی شده است و جمعآوری دادهها و تهیه گزارشهای دورهای مربوط به مقدار و نوع ضایعات به منظور شناسایی الگوهای بهبود انجام میشود. همچنین پیادهسازی روش تعریف پروژههای TQ برای شناسایی و کاهش ضایعات در دستور کار قرار گرفته است. در همین حال برگزاری دورههای آموزشی برای کارکنان در زمینه بهینهسازی مصرف مواد اولیه و کاهش ضایعات و تشویق کارکنان به ارائه ایدهها و راهکارهای نوآورانه در جهت کاهش ضایعات نیز از پیشبینیهای فولاد هرمزگان در قالب فرآیند تحلیل و مدیریت ضایعات است.
وی افزود: شرکت فولاد هرمزگان با استقرار نمایندگانی از واحد کنترل کیفیت در مبادی تأمین مواد اولیه و با انجام آزمایشات و کنترل کیفیت بر روی مواد اولیه در مبدأ و حین ورود مواد اولیه به کارخانه، برای اطمینان از عدم وجود ناخالصیها که ممکن است منجر به تولید ضایعات شود، اقدام کرده است و در این راستا ارتباطات مستمری نیز با تامین کنندگان خود داشته و جلسات مستمری را به صورت دورهای برگزار میکند. همچنین شرکت فولاد هرمزگان با شناسایی منابع تأمین جدید و بررسی آنالیزهای شیمیایی و فیزیکی محصولات هر کدام از منابع تأمین، متناسب با شرایط خطوط تولید خود، سعی در تأمین مواد اولیه با کیفیت دارد. همچنین در فرآیندی دیگر، مواد اولیه را از منابع جدید به صورت آزمایشی دریافت و مصرف و با بازخورد به تامینکنندگان در راستای افزایش کیفیت مواد خریداری شده، سعی در ایجاد منابع تامین پایدارتر میکند.
پیشبینی نیازهای مواد اولیه و بهبود فرآیند تولید
به گفته وی، همه ساله و قبل شروع سال جدید بررسیها و تحلیلهای دقیقی از نیازهای تولید به منظور جلوگیری از خرید اضافی مواد اولیه صورت میگیرد، متناسب با برنامه تعمیرات ماهیانه و سالیانه خطوط تولید و پارامترهای فنی، ظرفیت خطوط تولید مشخص شده و بر اساس نرخ مصارف مواد اولیه میزان نیاز به مواد اولیه برآورد و در طول سال نیز به صورت ماهیانه، هفتگی و روزانه میزان تولید و نرخ مصارف و نرخ تأمین و ورود مواد اولیه به شرکت و موجودی انبارها پایش و کنترل میشود.
ابوعطیوی در پایان تصریح کرد: استفاده از تجربیات و نظرات کارکنان در بهبود فرآیندهای استفاده از مواد اولیه میتواند تأثیر بسزایی بر کارایی، کیفیت و کاهش ضایعات داشته باشد؛ اقداماتی همچون ایجاد کانالهای ارتباطی موثر، ترویج فرهنگ مشارکت و تشویق ایدهپردازی، آموزش و توانمند سازی کارکنان و برگزاری دورههای آموزشی، ایجاد گروههای کاری و تشکیل تیمهای چند وظیفهای، نظارت و بازخورد نتایج و در نهایت توسعه پایدار شامل توجه به مسائل زیستمحیطی و ایجاد برنامههای پایش و بهبود مداوم میتوان اشاره کرد که در نهایت منجر به افزایش کارایی، افزایش انگیزه و رضایت شغلی کارکنان میشود.